|
ACCESS THE FULL ARTICLE
No SPIE Account? Create one
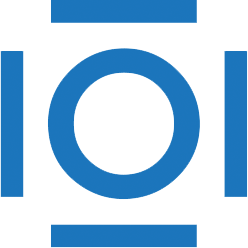
CITATIONS
Cited by 2 scholarly publications.
Microelectromechanical systems
Sensors
Packaging
Electrodes
Quartz
Semiconducting wafers
Capacitance