|
ACCESS THE FULL ARTICLE
No SPIE Account? Create one
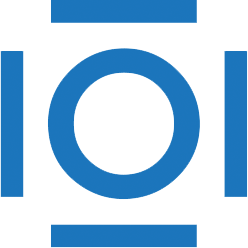
CITATIONS
Cited by 15 scholarly publications.
Photomasks
Glasses
Laser processing
Aluminum
Excimer lasers
Edge roughness
Photomicroscopy