|
ACCESS THE FULL ARTICLE
No SPIE Account? Create one
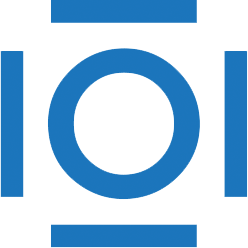
CITATIONS
Cited by 1 scholarly publication.
Photomasks
Inspection
Source mask optimization
Semiconducting wafers
Lithography
Manufacturing
Binary data