|
ACCESS THE FULL ARTICLE
No SPIE Account? Create one
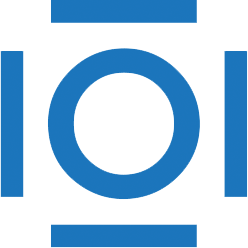
CITATIONS
Cited by 1 scholarly publication.
Laser welding
Solids
Carbon dioxide lasers
Chromium
Cladding
Resistance
Interfaces