For industrial three-dimensional (3D)-measuring applications as well as for other applications such as driver assistance systems in vehicles, a high-quality reproduction in a depth map calculation is of paramount importance. Yet to date, light field cameras still exhibit severe problems in imaging homogeneous surfaces such as smooth metallic surfaces, plastics, or semiconductor materials. On those, the necessary contrast for determining the topography is not present or too weak. Here, we present an innovative approach to improve the performance of light field cameras (also called plenoptic cameras) for various applications in 3D measurement technology. More specifically, we show that this disadvantage can be avoided using structured lighting pattern and analyze various lighting patterns (with respect to geometry, size, regularity, etc.) used to improve the performance of the algorithm in greater detail. In addition, different ways of projecting the pattern have been examined with regard to their advantages and disadvantages. We perform a systematic investigation of the impact of structured light illumination with regard to different object materials, object geometries, and illumination patterns as well as illumination sources. These examinations further comprise the analysis of environmental influences and magnitude of measurement deviations in a light field camera measuring set-up. Summing up, we investigated experimentally the influence of structured illumination on the performance of 3D depth information without the need of additional phase information. |
ACCESS THE FULL ARTICLE
No SPIE Account? Create one
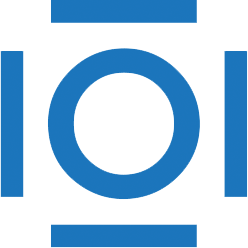
CITATIONS
Cited by 2 scholarly publications.
Cameras
Optical spheres
Beam splitters
Optical engineering
Specular reflections
Projection systems
3D metrology