|
ACCESS THE FULL ARTICLE
No SPIE Account? Create one
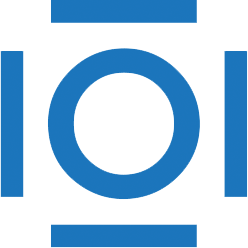
CITATIONS
Cited by 5 scholarly publications.
Microelectromechanical systems
Electrodes
Silicon
Video
Optical simulations
Solids
Scanning electron microscopy