|
ACCESS THE FULL ARTICLE
No SPIE Account? Create one
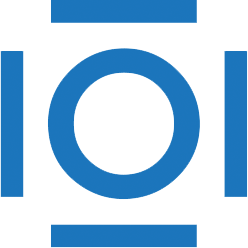
CITATIONS
Cited by 8 scholarly publications.
Photomasks
Lithography
Semiconducting wafers
Extreme ultraviolet
Extreme ultraviolet lithography
Manufacturing
Optical proximity correction