|
ACCESS THE FULL ARTICLE
No SPIE Account? Create one
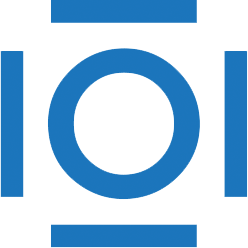
CITATIONS
Cited by 33 scholarly publications and 1 patent.
Directed self assembly
Semiconducting wafers
Etching
Critical dimension metrology
Inspection
Particles
Scanning electron microscopy